در فرآیند جوشکاری قوس الکتریکی با الکترود دستی (SMAW) یا همان جوشکاری “میگ” و “تیگ” مرسوم یکی از مشکلات رایج و آزاردهنده برای جوشکاران چسبیدن الکترود به قطعه کار است. این پدیده نه تنها فرآیند جوشکاری را مختل می کند و زمان بر است بلکه می تواند منجر به ایجاد عیوب جوش آسیب به تجهیزات و کاهش بهره وری شود. اما چرا الکترود می چسبد و چگونه می توان از بروز این مشکل جلوگیری کرد؟ در این مقاله به بررسی دقیق دلایل احتمالی چسبندگی الکترود و ارائه راهکارهای عملی برای پیشگیری از آن می پردازیم با تکیه بر اصول علمی و مهندسی جوشکاری و استانداردهای بین المللی مرتبط.
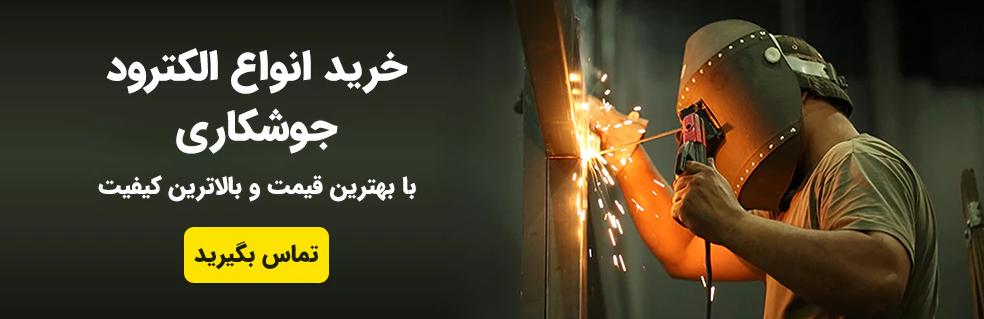
منبع: https://industryalloy.com
تعریف و عملکرد فنی چسبندگی الکترود
چسبندگی الکترود در جوشکاری قوس الکتریکی به وضعیتی اطلاق می شود که نوک الکترود به قطعه کار ذوب شده و به آن متصل می گردد به گونه ای که جدا کردن الکترود بدون خاموش کردن دستگاه جوش و ضربه زدن به نگهدارنده الکترود دشوار یا غیرممکن می شود. این پدیده زمانی رخ می دهد که انتقال حرارت و مذاب بین الکترود و قطعه کار به درستی انجام نگیرد و یا نیروهای سطحی و متالورژیکی نامطلوبی در ناحیه قوس الکتریکی ایجاد شود.
از نظر فنی در فرآیند جوشکاری قوس الکتریکی یک قوس الکتریکی پایدار بین الکترود و قطعه کار ایجاد می شود. این قوس الکتریکی با یونیزه کردن گاز محافظ (در صورت وجود) و ایجاد پلاسمای حرارتی حرارت لازم برای ذوب الکترود و سطح قطعه کار را فراهم می کند. مذاب الکترود به صورت قطرات ریز به حوضچه مذاب قطعه کار منتقل شده و پس از انجماد اتصال جوش را ایجاد می کند. عملکرد صحیح این فرآیند به عوامل متعددی از جمله تنظیمات جریان و ولتاژ نوع الکترود تکنیک جوشکاری و شرایط سطحی قطعه کار بستگی دارد. چسبندگی الکترود نشان دهنده اختلال در این فرآیند و عدم تعادل پارامترهای جوشکاری است.
اجزای اصلی و اصول کارکرد جوشکاری قوس الکتریکی
برای درک بهتر دلایل چسبندگی الکترود لازم است با اجزای اصلی و اصول کارکرد سیستم جوشکاری قوس الکتریکی آشنا شویم. یک سیستم جوشکاری قوس الکتریکی معمولاً از اجزای زیر تشکیل شده است :
- منبع تغذیه جوشکاری (Power Source) : تامین کننده جریان و ولتاژ الکتریکی مورد نیاز برای ایجاد قوس الکتریکی. منابع تغذیه می توانند از نوع جریان ثابت (CC) یا ولتاژ ثابت (CV) باشند که هر کدام برای فرآیندهای جوشکاری خاصی مناسب هستند. در جوشکاری SMAW معمولاً از منابع تغذیه جریان ثابت استفاده می شود. منابع تغذیه مدرن قابلیت های پیشرفته ای مانند جوشکاری پالسی و کنترل شکل موج را نیز ارائه می دهند که می توانند در کاهش چسبندگی الکترود موثر باشند.
- نگهدارنده الکترود (Electrode Holder) : وسیله ای عایق برای نگهداری و هدایت الکترود جوشکاری. نگهدارنده الکترود باید به گونه ای طراحی شده باشد که عایق الکتریکی مناسب را فراهم کرده و در عین حال امکان تعویض آسان الکترود را فراهم کند. همچنین باید جریان جوشکاری را به طور موثر به الکترود منتقل کند.
- الکترود جوشکاری (Welding Electrode) : ماده مصرفی که هم به عنوان رسانای جریان الکتریکی و هم به عنوان ماده پرکننده در فرآیند جوشکاری عمل می کند. الکترودها بر اساس نوع پوشش ترکیب شیمیایی و کاربرد دسته بندی می شوند. پوشش الکترود نقش مهمی در ایجاد گاز محافظ پایداری قوس الکتریکی و خواص متالورژیکی جوش دارد. انتخاب الکترود مناسب با توجه به نوع فلز پایه و شرایط جوشکاری از عوامل کلیدی در جلوگیری از چسبندگی است. استانداردهایی مانند AWS A۵.۱ و AWS A۵.۵ به دسته بندی و مشخصات الکترودهای جوشکاری می پردازند.
- کابل های جوشکاری (Welding Cables) : انتقال جریان الکتریکی از منبع تغذیه به نگهدارنده الکترود و قطعه کار. کابل ها باید از رسانای قوی و عایق مناسب ساخته شده باشند و قطر مناسب برای جریان جوشکاری را داشته باشند. کابل های نامناسب یا اتصالات ضعیف می توانند منجر به افت ولتاژ و جریان شده و در نتیجه بر پایداری قوس و احتمال چسبندگی الکترود تاثیر بگذارند.
- گیره اتصال زمین (Work Clamp) : اتصال قطعه کار به مدار جوشکاری. گیره اتصال زمین باید اتصال الکتریکی مطمئن و با سطح تماس کافی را فراهم کند تا از افت جریان و ایجاد قوس های ناخواسته جلوگیری شود.
- قطعه کار (Workpiece) : قطعه یا قطعاتی که قرار است به یکدیگر جوش داده شوند. جنس ضخامت تمیزی سطح و دمای قطعه کار از عوامل موثر بر فرآیند جوشکاری و احتمال چسبندگی الکترود هستند.
اصول کارکرد جوشکاری قوس الکتریکی بر پایه ایجاد قوس الکتریکی پایدار استوار است. هنگامی که الکترود به قطعه کار نزدیک می شود جریان الکتریکی از طریق الکترود و قوس الکتریکی به قطعه کار منتقل می شود. مقاومت الکتریکی هوا و گاز محافظ در مسیر قوس باعث افزایش دما تا هزاران درجه سانتیگراد می شود. این حرارت بالا باعث ذوب لبه های قطعه کار و نوک الکترود می شود. پوشش الکترود در حین سوختن گاز محافظی را تولید می کند که از حوضچه مذاب در برابر آلودگی های اتمسفری محافظت می کند. همچنین پوشش الکترود شار را نیز تامین می کند که به تمیز کردن سطح فلز مذاب و بهبود خواص جوش کمک می کند. مهارت جوشکار در حفظ فاصله قوس الکتریکی مناسب زاویه الکترود و سرعت پیشروی نقش حیاتی در ایجاد جوش با کیفیت و جلوگیری از چسبندگی الکترود دارد.
دلایل اصلی چسبندگی الکترود
چسبندگی الکترود می تواند به دلایل متعددی رخ دهد که در ادامه به مهم ترین آن ها اشاره می شود :
۱. جریان جوشکاری نامناسب (جریان پایین)
یکی از شایع ترین دلایل چسبندگی الکترود تنظیم جریان جوشکاری بسیار پایین است. جریان پایین حرارت کافی برای ذوب مناسب الکترود و قطعه کار را فراهم نمی کند. در نتیجه الکترود به جای ذوب شدن و تشکیل حوضچه مذاب به سطح قطعه کار می چسبد. انتخاب جریان مناسب بستگی به نوع و قطر الکترود ضخامت قطعه کار و نوع اتصال جوش دارد. جدول های مشخصات الکترود و دستورالعمل های جوشکاری معمولاً محدوده جریان مناسب برای هر الکترود را مشخص می کنند. استفاده از آمپرمتر کلمپی برای اطمینان از تنظیم صحیح جریان جوشکاری توصیه می شود.
۲. طول قوس الکتریکی نامناسب
طول قوس الکتریکی فاصله بین نوک الکترود و سطح قطعه کار است. قوس الکتریکی خیلی کوتاه (تماس مستقیم الکترود با قطعه کار) باعث می شود الکترود به سرعت گرم شده و به قطعه کار بچسبد. از طرف دیگر قوس الکتریکی خیلی بلند نیز می تواند منجر به ناپایداری قوس کاهش انتقال حرارت و افزایش پاشش مذاب شود. طول قوس الکتریکی ایده آل معمولاً برابر با قطر الکترود یا کمی کمتر است. جوشکار باید با مهارت و دقت طول قوس را در حین جوشکاری حفظ کند. تمرین و تجربه نقش کلیدی در تسلط بر این مهارت دارند.
۳. زاویه نامناسب الکترود
زاویه الکترود نسبت به قطعه کار نیز بر انتقال حرارت و پایداری قوس تاثیرگذار است. زاویه نامناسب می تواند منجر به توزیع نامناسب حرارت ذوب ناهمگن و در نتیجه چسبندگی الکترود شود. زاویه جوشکاری بستگی به نوع اتصال جوش موقعیت جوشکاری و نوع الکترود دارد. به طور کلی برای جوشکاری تخت و افقی زاویه ۹۰ درجه یا کمی مایل به سمت جلو (زاویه کششی) توصیه می شود. برای جوشکاری سربالا و بالای سر زاویه کمی مایل به سمت عقب (زاویه فشاری) ممکن است مناسب تر باشد. دستورالعمل های جوشکاری و راهنمایی های سازندگان الکترود معمولاً زوایای توصیه شده را برای کاربردهای مختلف ارائه می دهند.
۴. نوع نامناسب الکترود
استفاده از الکترود نامناسب برای نوع فلز پایه یا شرایط جوشکاری می تواند به چسبندگی الکترود منجر شود. الکترودها بر اساس ترکیب شیمیایی نوع پوشش و کاربرد دسته بندی می شوند. به عنوان مثال الکترودهای سلولزی برای جوشکاری فولادهای کم کربن و الکترودهای روتیلی برای جوشکاری ورق های نازک مناسب هستند. استفاده از الکترود نامناسب می تواند منجر به عدم سازگاری متالورژیکی پایداری ضعیف قوس و چسبندگی الکترود شود. انتخاب الکترود مناسب با توجه به نوع فلز پایه ضخامت موقعیت جوشکاری و خواص مکانیکی مورد نیاز ضروری است. استانداردهای AWS A۵.۱ و AWS A۵.۵ و کاتالوگ های سازندگان الکترود منابع ارزشمندی برای انتخاب الکترود مناسب هستند.
۵. سطح نامناسب قطعه کار
سطح قطعه کار باید تمیز و عاری از هرگونه آلودگی مانند زنگ زدگی روغن گریس رنگ رطوبت و پوسته های اکسیدی باشد. این آلودگی ها می توانند پایداری قوس الکتریکی را مختل کرده انتقال حرارت را کاهش داده و باعث چسبندگی الکترود شوند. آماده سازی سطح قطعه کار شامل سنگ زنی برس زنی سیمی سندبلاست یا شستشو با حلال های مناسب قبل از جوشکاری ضروری است. به ویژه در جوشکاری فولادهای زنگ نزن و آلومینیوم تمیزی سطح از اهمیت ویژه ای برخوردار است. استاندارد ISO ۱۲۹۴۴–۴ به روش های آماده سازی سطح فولاد قبل از رنگ آمیزی و جوشکاری می پردازد که اصول کلی آن برای آماده سازی سطح قبل از جوشکاری نیز قابل استفاده است.
۶. تکنیک جوشکاری نامناسب
تکنیک جوشکاری نقش مهمی در جلوگیری از چسبندگی الکترود دارد. حرکات نامناسب الکترود سرعت پیشروی زیاد یا کم و عدم حفظ قوس الکتریکی پایدار می تواند منجر به چسبندگی شود. تکنیک های مختلف جوشکاری مانند جوشکاری رفت و برگشتی دایره ای و زیگزاگی برای کاربردهای مختلف وجود دارد. انتخاب تکنیک مناسب و اجرای صحیح آن نیازمند مهارت و تجربه جوشکار است. آموزش های جوشکاری و تمرین های عملی برای بهبود تکنیک جوشکاری و کاهش احتمال چسبندگی الکترود ضروری هستند.
۷. گرمای بیش از حد الکترود
گرمای بیش از حد الکترود می تواند ناشی از جریان جوشکاری خیلی بالا سرعت پیشروی خیلی کم یا استفاده از الکترود با قطر خیلی کوچک باشد. الکترود بیش از حد گرم شده به سرعت ذوب شده و احتمال چسبندگی آن به قطعه کار افزایش می یابد. انتخاب پارامترهای جوشکاری مناسب و رعایت سرعت پیشروی توصیه شده برای جلوگیری از گرمای بیش از حد الکترود ضروری است. در صورت استفاده از جریان بالا باید از الکترود با قطر بزرگتر استفاده شود تا جریان به طور مناسب توزیع شده و از گرمای بیش از حد جلوگیری شود.
۸. پدیده قوس مغناطیسی (Arc Blow)
قوس مغناطیسی پدیده ای است که در جوشکاری با جریان مستقیم (DC) رخ می دهد به ویژه در جوشکاری فولادهای مغناطیسی و در گوشه ها و اتصالات ضخیم. میدان مغناطیسی ایجاد شده توسط جریان جوشکاری می تواند قوس الکتریکی را از مسیر اصلی خود منحرف کند و باعث ناپایداری قوس پاشش مذاب و چسبندگی الکترود شود. برای کاهش قوس مغناطیسی می توان از جریان متناوب (AC) به جای جریان مستقیم استفاده کرد اتصال زمین را به قطعه کار نزدیک تر کرد یا از تکنیک های جوشکاری خاص مانند جوشکاری گام به گام استفاده نمود. همچنین کاهش جریان جوشکاری نیز می تواند در کاهش اثر قوس مغناطیسی موثر باشد.
کاربردهای صنعتی و مثال هایی از صنایع مختلف
جوشکاری قوس الکتریکی با الکترود دستی (SMAW) به دلیل سادگی قابلیت حمل و انعطاف پذیری در صنایع مختلف کاربردهای گسترده ای دارد. با این حال چسبندگی الکترود می تواند در برخی از این کاربردها مشکلات جدی ایجاد کند. برخی از صنایع و کاربردهای مهم جوشکاری SMAW عبارتند از :
- صنعت ساخت و ساز : جوشکاری سازه های فلزی پل ها ساختمان ها مخازن و لوله ها. در این صنعت جوشکاری در موقعیت های مختلف (تخت افقی سربالا و بالای سر) انجام می شود و چسبندگی الکترود در موقعیت های دشوار می تواند کارایی جوشکار را به شدت کاهش دهد.
- صنعت کشتی سازی : جوشکاری بدنه کشتی ها سکوهای دریایی و تجهیزات بندری. در این صنعت حجم جوشکاری بسیار زیاد است و چسبندگی الکترود می تواند زمان تعمیرات و هزینه ها را افزایش دهد.
- صنعت خودروسازی : جوشکاری قطعات شاسی و بدنه خودروها. در خطوط تولید خودکار توقف فرآیند جوشکاری به دلیل چسبندگی الکترود می تواند منجر به اختلال در کل خط تولید شود.
- صنعت نفت و گاز : جوشکاری خطوط لوله انتقال نفت و گاز مخازن تحت فشار و تجهیزات پالایشگاهی. در این صنعت کیفیت و ایمنی جوشکاری از اهمیت بالایی برخوردار است و چسبندگی الکترود می تواند منجر به عیوب جوش و کاهش استحکام اتصالات شود.
- صنعت تعمیر و نگهداری : تعمیرات ماشین آلات صنعتی تجهیزات کشاورزی و خودروها. در این صنعت تنوع قطعات و شرایط جوشکاری بسیار زیاد است و جوشکار باید بتواند با شرایط مختلف سازگار شود و از چسبندگی الکترود جلوگیری کند.
مثال های صنعتی :
- در ساخت پل های فولادی جوشکاری اتصالات تیرها و ستون ها در ارتفاعات انجام می شود. چسبندگی الکترود در این شرایط می تواند خطرناک و زمان بر باشد.
- در تعمیر خطوط لوله نفت و گاز جوشکاری در شرایط محیطی سخت و در موقعیت های محدود انجام می شود. چسبندگی الکترود می تواند فرآیند تعمیر را طولانی و پرهزینه کند.
- در خطوط تولید خودرو جوشکاری رباتیک با الکترود دستی نیز کاربرد دارد. توقف ربات به دلیل چسبندگی الکترود می تواند تولید را متوقف کند و خسارات زیادی به بار آورد.
بررسی استانداردهای بین المللی و فناوری های پیشرفته مرتبط
استانداردهای بین المللی نقش مهمی در تضمین کیفیت جوشکاری و ایمنی فرآیند دارند. استانداردهای مختلفی در زمینه جوشکاری قوس الکتریکی و الکترودهای جوشکاری وجود دارد که به طور غیرمستقیم به موضوع چسبندگی الکترود نیز مرتبط می شوند. برخی از استانداردهای مهم عبارتند از :
- ISO ۳۸۳۴ : الزامات کیفیت برای جوشکاری ذوبی مواد فلزی : این استاندارد به الزامات سیستم مدیریت کیفیت در جوشکاری می پردازد و شامل بخش هایی در مورد انتخاب مواد مصرفی روش های جوشکاری квалификация پرسنل و بازرسی جوش است. رعایت این استاندارد می تواند به بهبود کیفیت جوشکاری و کاهش مشکلات مربوط به چسبندگی الکترود کمک کند.
- ISO ۹۶۰۶ : آزمون квалификации جوشکاران ذوبی : این استاندارد به روش های آزمون صلاحیت جوشکاران برای جوشکاری ذوبی فلزات می پردازد. جوشکاران квалифицированный با مهارت و تجربه کافی احتمال کمتری برای بروز مشکل چسبندگی الکترود دارند.
- AWS A۵.۱/A۵.۱M : مشخصات الکترودهای فولاد کربنی برای جوشکاری قوس الکتریکی با پوشش : این استاندارد به مشخصات فنی و دسته بندی الکترودهای فولاد کربنی مورد استفاده در جوشکاری SMAW می پردازد. انتخاب الکترود مناسب بر اساس این استاندارد می تواند به بهبود کیفیت جوشکاری و کاهش چسبندگی الکترود کمک کند.
- AWS A۵.۵/A۵.۵M : مشخصات الکترودهای فولاد کم آلیاژ برای جوشکاری قوس الکتریکی با پوشش : این استاندارد مشابه AWS A۵.۱ است اما برای الکترودهای فولاد کم آلیاژ.
فناوری های پیشرفته مرتبط :
- منابع تغذیه جوشکاری دیجیتال با کنترل شکل موج : این منابع تغذیه قابلیت کنترل دقیق تر جریان و ولتاژ جوشکاری را فراهم می کنند و می توانند برای بهینه سازی فرآیند جوشکاری و کاهش چسبندگی الکترود مورد استفاده قرار گیرند. قابلیت هایی مانند جوشکاری پالسی و شروع نرم قوس (Soft Start) در این منابع تغذیه می تواند به کاهش احتمال چسبندگی در ابتدای جوشکاری کمک کند.
- سیستم های پایش فرآیند جوشکاری : این سیستم ها با استفاده از سنسورها و نرم افزارهای پیشرفته پارامترهای جوشکاری را به طور پیوسته پایش می کنند و در صورت بروز انحراف از مقادیر مطلوب به جوشکار هشدار می دهند. این سیستم ها می توانند به تشخیص زودهنگام مشکلات مربوط به چسبندگی الکترود و جلوگیری از بروز آن کمک کنند.
- الکترودهای با پوشش بهبود یافته : تولیدکنندگان الکترود به طور مداوم در حال بهبود فرمولاسیون پوشش الکترودها هستند تا خواص جوشکاری آن ها را بهبود بخشند و مشکل چسبندگی را کاهش دهند. الکترودهای جدید با پوشش های پیشرفته تر می توانند پایداری قوس الکتریکی را افزایش داده انتقال مذاب را بهبود بخشند و احتمال چسبندگی را کاهش دهند.
چالش ها و محدودیت های فنی
با وجود پیشرفت های فناوری در زمینه جوشکاری چسبندگی الکترود همچنان می تواند یک چالش فنی در برخی از کاربردها باشد. برخی از چالش ها و محدودیت های فنی مرتبط با این موضوع عبارتند از :
- مهارت جوشکار : جوشکاری SMAW همچنان به مهارت و تجربه جوشکار وابسته است. خطای انسانی در تنظیم پارامترهای جوشکاری تکنیک جوشکاری و حفظ قوس الکتریکی پایدار می تواند منجر به چسبندگی الکترود شود. آموزش و квалификация مناسب جوشکاران برای کاهش این چالش ضروری است.
- شرایط محیطی : شرایط محیطی نامساعد مانند باد شدید رطوبت بالا و دمای بسیار پایین یا بالا می تواند بر فرآیند جوشکاری تاثیر گذاشته و احتمال چسبندگی الکترود را افزایش دهد. محافظت از ناحیه جوشکاری در برابر باد و رطوبت و تنظیم پارامترهای جوشکاری با توجه به دما می تواند به کاهش این چالش کمک کند.
- جوشکاری در موقعیت های دشوار : جوشکاری در موقعیت های سربالا و بالای سر و در فضاهای محدود به دلیل دسترسی محدود و دید نامناسب دشوارتر است و احتمال چسبندگی الکترود در این موقعیت ها بیشتر است. استفاده از تکنیک های جوشکاری خاص و تجهیزات کمکی می تواند به بهبود شرایط جوشکاری در این موقعیت ها کمک کند.
- تنوع مواد و الکترودها : تنوع بسیار زیاد مواد فلزی و الکترودهای جوشکاری انتخاب الکترود و پارامترهای جوشکاری مناسب را پیچیده می کند. عدم تطابق الکترود با فلز پایه یا شرایط جوشکاری می تواند منجر به چسبندگی الکترود شود. استفاده از راهنمایی های سازندگان الکترود و استانداردهای مربوطه برای انتخاب مناسب ضروری است.
- پدیده قوس مغناطیسی : پدیده قوس مغناطیسی به ویژه در جوشکاری با جریان مستقیم و در اتصالات ضخیم و گوشه ها همچنان یک چالش است و می تواند باعث چسبندگی الکترود شود. استفاده از جریان متناوب تغییر قطبیت جریان و تکنیک های جوشکاری خاص برای کاهش اثر قوس مغناطیسی توصیه می شود.
نکات کلیدی برای جلوگیری از چسبندگی الکترود و بهینه سازی عملکرد
برای جلوگیری از چسبندگی الکترود و بهینه سازی عملکرد جوشکاری SMAW رعایت نکات زیر ضروری است :
- انتخاب الکترود مناسب : الکترود را با توجه به نوع فلز پایه ضخامت موقعیت جوشکاری و خواص مکانیکی مورد نیاز انتخاب کنید. به دستورالعمل های سازندگان الکترود و استانداردهای مربوطه توجه کنید.
- تنظیم جریان جوشکاری مناسب : جریان جوشکاری را بر اساس قطر الکترود نوع اتصال جوش و ضخامت قطعه کار تنظیم کنید. از جدول های مشخصات الکترود و دستورالعمل های جوشکاری استفاده کنید. در صورت لزوم جریان را به تدریج افزایش دهید تا به جریان مناسب برسید.
- حفظ طول قوس الکتریکی مناسب : طول قوس الکتریکی را به طور مداوم کنترل کنید و آن را در محدوده قطر الکترود یا کمی کمتر نگه دارید. تمرین و تجربه در حفظ طول قوس الکتریکی مناسب نقش کلیدی دارد.
- رعایت زاویه مناسب الکترود : زاویه الکترود را با توجه به نوع اتصال جوش و موقعیت جوشکاری تنظیم کنید. به دستورالعمل های جوشکاری توجه کنید.
- آماده سازی سطح قطعه کار : سطح قطعه کار را قبل از جوشکاری به طور کامل تمیز کنید و هرگونه آلودگی را از بین ببرید. از روش های مناسب آماده سازی سطح مانند سنگ زنی برس زنی سیمی یا سندبلاست استفاده کنید.
- استفاده از تکنیک جوشکاری مناسب : تکنیک جوشکاری مناسب را با توجه به نوع اتصال جوش و موقعیت جوشکاری انتخاب کنید و به درستی اجرا کنید. آموزش های جوشکاری و تمرین های عملی برای بهبود تکنیک جوشکاری ضروری هستند.
- جلوگیری از گرمای بیش از حد الکترود : پارامترهای جوشکاری را به گونه ای تنظیم کنید که از گرمای بیش از حد الکترود جلوگیری شود. در صورت استفاده از جریان بالا از الکترود با قطر بزرگتر استفاده کنید و سرعت پیشروی مناسب را رعایت کنید.
- کاهش اثر قوس مغناطیسی : در صورت بروز پدیده قوس مغناطیسی از جریان متناوب (AC) به جای جریان مستقیم (DC) استفاده کنید اتصال زمین را به قطعه کار نزدیک تر کنید یا از تکنیک های جوشکاری خاص استفاده نمایید.
- بررسی و نگهداری تجهیزات جوشکاری : تجهیزات جوشکاری را به طور منظم بررسی و نگهداری کنید. از سلامت کابل های جوشکاری نگهدارنده الکترود و گیره اتصال زمین اطمینان حاصل کنید. اتصالات الکتریکی را تمیز و محکم نگه دارید.
- تمرین و کسب تجربه : تمرین مداوم و کسب تجربه عملی بهترین راه برای بهبود مهارت جوشکاری و کاهش احتمال چسبندگی الکترود است. آموزش های جوشکاری و کارگاه های آموزشی می توانند در این زمینه بسیار مفید باشند.
نتیجه گیری علمی و تخصصی
چسبندگی الکترود در جوشکاری قوس الکتریکی با الکترود دستی (SMAW) یک مشکل رایج است که می تواند فرآیند جوشکاری را مختل کرده و کیفیت جوش را کاهش دهد. دلایل اصلی چسبندگی الکترود شامل جریان جوشکاری نامناسب (پایین) طول قوس الکتریکی نامناسب زاویه نامناسب الکترود نوع نامناسب الکترود سطح نامناسب قطعه کار تکنیک جوشکاری نامناسب گرمای بیش از حد الکترود و پدیده قوس مغناطیسی است.
جلوگیری از چسبندگی الکترود نیازمند درک عمیق اصول جوشکاری قوس الکتریکی انتخاب صحیح مواد مصرفی تنظیم دقیق پارامترهای جوشکاری آماده سازی مناسب قطعه کار اجرای صحیح تکنیک جوشکاری و مهارت و تجربه جوشکار است. رعایت نکات کلیدی ارائه شده در این مقاله و بهره گیری از استانداردهای بین المللی و فناوری های پیشرفته می تواند به طور قابل توجهی احتمال چسبندگی الکترود را کاهش داده و عملکرد جوشکاری SMAW را بهینه سازی کند.
تحقیقات و توسعه در زمینه مواد مصرفی و تجهیزات جوشکاری همچنان ادامه دارد و هدف آن بهبود خواص جوشکاری افزایش بهره وری و کاهش مشکلات فنی مانند چسبندگی الکترود است. استفاده از الکترودهای با پوشش های پیشرفته تر منابع تغذیه جوشکاری دیجیتال با کنترل شکل موج و سیستم های پایش فرآیند جوشکاری از جمله فناوری هایی هستند که می توانند در آینده نقش مهمی در کاهش چالش های جوشکاری SMAW ایفا کنند.
پرسش و پاسخ (FAQ)
۱. چرا وقتی الکترود برای اولین بار به قطعه کار می چسبد جدا کردن آن سخت است؟
هنگامی که الکترود به قطعه کار می چسبد جریان جوشکاری همچنان برقرار است و حرارت تولید می شود. این حرارت باعث ذوب بیشتر الکترود و سطح قطعه کار در نقطه تماس می شود و اتصال مذاب قوی تری بین آن ها ایجاد می گردد. به همین دلیل جدا کردن الکترود بدون خاموش کردن دستگاه جوش و ضربه زدن به نگهدارنده الکترود دشوار است. خاموش کردن دستگاه جوش بلافاصله پس از چسبیدن الکترود می تواند به کاهش شدت اتصال و سهولت جدا کردن آن کمک کند.
۲. آیا استفاده از الکترودهای خاصی می تواند از چسبندگی جلوگیری کند؟
بله برخی از الکترودها به گونه ای طراحی شده اند که احتمال چسبندگی کمتری داشته باشند. به عنوان مثال الکترودهای با پوشش روتیلی به دلیل قوس الکتریکی نرم تر و پاشش مذاب کمتر معمولاً کمتر از الکترودهای سلولزی به قطعه کار می چسبند. همچنین الکترودهای استنلس استیل به دلیل مذاب روان تر ممکن است بیشتر مستعد چسبندگی باشند. انتخاب الکترود مناسب با توجه به نوع فلز پایه و شرایط جوشکاری و رعایت پارامترهای جوشکاری توصیه شده می تواند به کاهش احتمال چسبندگی کمک کند.
۳. چگونه می توان از چسبیدن الکترود در هنگام شروع جوشکاری جلوگیری کرد؟
چسبیدن الکترود در هنگام شروع جوشکاری بسیار رایج است به ویژه برای جوشکاران مبتدی. برای جلوگیری از این مشکل می توان از روش های زیر استفاده کرد :
- استفاده از جریان جوشکاری کمی بالاتر در ابتدای جوشکاری : افزایش جزئی جریان در لحظه شروع می تواند به ایجاد سریع تر قوس الکتریکی و ذوب مناسب الکترود کمک کند. پس از برقراری قوس پایدار می توان جریان را به مقدار تنظیم شده کاهش داد.
- استفاده از تکنیک ضربه زدن (Tapping) : به جای کشیدن الکترود روی سطح قطعه کار به آرامی نوک الکترود را به سطح قطعه کار ضربه بزنید تا قوس الکتریکی ایجاد شود. این روش می تواند از چسبیدن الکترود در لحظه تماس اولیه جلوگیری کند.
- استفاده از منابع تغذیه جوشکاری با قابلیت شروع نرم قوس (Soft Start) : این منابع تغذیه جریان جوشکاری را به تدریج افزایش می دهند و از ایجاد جریان ناگهانی و چسبیدن الکترود در ابتدای جوشکاری جلوگیری می کنند.
- تمرین و کسب تجربه : با تمرین مداوم و کسب تجربه عملی جوشکار می تواند حساسیت لمسی و هماهنگی چشم و دست خود را بهبود بخشیده و مهارت لازم برای شروع موفقیت آمیز جوشکاری بدون چسبیدن الکترود را کسب کند.